
Share your ideas. Tell us your stories. Join the Instron Community.
Welcome to our new Instron Community Blog hosted by Instron. It is a compilation of the freshest, brightest, most-talented minds that Instron has to offer. The world of materials science is so vast and encompasses the broadest range of industries, materials, and challenges that no one person can possibly possess all the knowledge required to be the resident expert – or master of materials science. It takes a small army behind the scenes collaborating and sharing technical know-how, experiences, and ideas to present the most accurate, relevant, and timely information to you – our readers.
We invite you to tell us who you are, share your stories and talk about your experiences. Join the Instron Community.
We invite you to tell us who you are, share your stories and talk about your experiences. Join the Instron Community.
Tuesday, June 26, 2012
Costco Tests Most Valued Product with an Instron System
Since 1983, Costco has become the largest membership warehouse chain in the United States. The company profits $1.5 billion annually in over 170 stores throughout 7 countries, with plans to double its footprint over the next decade. In its own testing lab, an Instron 3343 with pneumatic grips can be found testing Costco’s most valued product. A recent business documentary by CNBC profiles the retailer and the consumer "craze" it's ignited.
Read more

Thursday, June 21, 2012
Damascus Swords - An Ancient Advanced Material
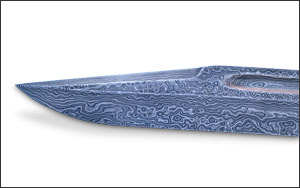
Damascus blades, first encountered by Europeans in the Middle Ages in the Middle East and Asia, had features not found in European steels: extraordinary mechanical properties, an exceptionally sharp cutting edges, and a damask pattern.
Damascus blades were forged from Wootz steel from India. India has been reputed for its iron and steel since ancient times. Literary accounts indicate that steel from southern India was rated as some of the finest in the world and was traded throughout Europe, China, and the Middle East.
Steel is made by alloying iron with carbon. High carbon contents of 1 - 2% make the material hard, but also make it brittle. This property is useless for sword making since the blade would shatter upon impact with a shield or another sword. However, Wootz steel, with a carbon content of about 1.5%, showed a seemingly impossible combination of hardness and malleability.
According to an early report on Indian Wootz steel production, iron ores taken from particular mines in India contained small traces of impurities; the metals including vanadium, chromium, manganese, cobalt and nickel. Other particular ingredients were necessary in the smelting process: wood from Cassia auriculata and leaves of Calotropis gigantea.
Wootz steel was produced as small ingots and shipped to Damascus, Syria, where bladesmiths learned to forge them into the swords that displayed a beautiful surface pattern. The high carbon level of these steels plays a key role in producing the characteristic surface pattern because the pattern results from alignment of the cementite (Fe3C) particles that form in such steels on cooling.
Unfortunately, production of Damascus swords gradually declined, ceasing by around 1750, and the process was lost to bladesmiths. Several theories have been put forward for this decline, such as exhaustion of the supply of iron ore of the correct composition, disturbance of trade routes, and loss of knowledge of the smithing process through secrecy over time.
Nowadays, the term Damascus steel refers to two different types; one of which is the true ancient Wootz Damascus steel with a texture originating from the etched crystalline structure, the other is a composite structure made by welding, folding, and twisting of alternating layers of iron and steel to give a visible pattern on the surface of the final blade.
The legends associated with the excellent properties of Wootz steel and the beautiful patterns on Damascus blades caught the imagination of European scientists in the 17th through 19th centuries since the use of high-carbon iron alloys was not really known previously in Europe and hence played an important role in the development of modern metallurgy. Textured Damascus steel was one of the earliest materials to be examined at the microstructure level.
Both the internal microstructure and the chemical composition of these steels were well established by the early 1900s. The internal microstructure of a Wootz Damascus blade possessing a high-quality damascene surface pattern consists of bands of small particles of cementite clustered along the band centerline. The bands have a characteristic spacing of 30 to 70 mm and are contained in a steel matrix. The bands lie parallel to the forging plane of the blades. By manipulating the angle of the blade surface, relative to the plane of the bands, the bladesmith can produce a variety of convoluted patterns of intersection of the bands with the blade surface. After polishing and etching, the cementite bands appear white and the steel matrix nearly black, creating the surface pattern.
More recently, materials researcher Peter Paufler and his colleagues at Dresden University (Germany) using high-resolution transmission electron microscopy, have detected carbon nanotubes in a specimen taken from a genuine Damascus sabre produced by the famous blacksmith Assad Ullah in the 17th century. The nanotubes appear after dissolution of the sample in hydrochloric acid. Incompletely dissolved cementite nanowires were also identified, indicating that these wires could have been encapsulated and protected by the carbon nanotubes.
Carbon nanotubes are cylinders made of hexagonally-arranged carbon atoms. They are among the strongest materials known and have great elasticity and tensile strength. The team theorizes that the nanotubes were protecting nanowires of hard and brittle cementite. That may be the answer to the steel’s special properties; at a nanometer level, it is a composite material. The malleability of the carbon nanotubes compensates for the brittleness of the cementite formed by the high-carbon Wootz steel.
It is not clear how ancient bladesmiths produced these nanotubes, but the researchers believe that the key to this process lay with the unique combination of impurities in the Wootz. Alternating temperature phases during manufacture caused these impurities to segregate out into planes. From there, they would have acted as catalysts for the formation of the carbon nanotubes, which in turn would have promoted the formation of the cementite nanowires.
Using the unique properties of Wootz steel, and their unique blade-treatment procedures, Syrian craftsmen may have been making that most modern of material, carbon nanotubes, more than 400 years ago.
Sources: Wootz Steel: An Advanced Material Of The Ancient World. Updated November, 18th 2000. S. Srinivasan and S. Ranganathan. Department of Metallurgy, Indian Institute of Science, Bangalore.
The Key Role of Impurities in Ancient Damascus Steel Blades J.D. Verhoeven, A.H. Pendray, and W.E. Dauksch JOM, 50 (9) (1998).
Carbon Nanotubes in an Ancient Damascus Sabre. NATURE, Vol 444, 16 November 2006. Read more

LABELS:
Featured Posts,
Metals
Thursday, June 14, 2012
Ensuring Top Quality When Reinventing the Wheel
Picture a world without grocery carts, hospital beds without the versatility of motion, or luggage that must always be carried. As customer Tente aims to make everyday tasks painless by continuing to redefine the age-old wheel, Instron’s equipment is right there verifying performance and longevity. Imagine a world without the wheel and take a look at the processes that take place before the end consumer enjoys its many functions.
Read more

Friday, June 8, 2012
Resolving the Issue of Seam Slippage in Tensile Testing
When evaluating seam strength and seam integrity in tensile testing, seam slippage can occur. Under a certain load, the warp and weft threads of a sewn seam start pulling away before the fabric itself ruptures. Due to this byproduct, the effect of fabric stretching needs to be "subtracted" from the equation. Learn how you can use Bluehill® testing software’s seam slippage calculation to easily account for this.
Read more

LABELS:
Software
Wednesday, June 6, 2012
Instron Exhibits at the World Biomaterials Congress in China
Instron continues to focus on global trends, and this week biomaterials was at the center. Instron and its ElectroPuls machine traveled to the city of Chengdu to visit the World Biomaterials Congress. With offices in Beijing and Shanghai, Chengdu is also important to Instron as it is considered the Chinese "hub" of biomaterials research and development and full of potential opportunities. Its many universities and research institutions offer strong technological and human resources support. Learn more about Instron’s experience at the exposition and the new trends in the biomaterials world.
Read more

LABELS:
Biomedical,
Featured Posts,
Products
Friday, June 1, 2012
Instron Strengthens Community through the United Way
Instron’s parent company, Illinois Tool Works (ITW), has accepted United Way’s top global honor, the Summit Award, in recognition for its efforts in the 2011-2012 campaign. The Spirit of America and Summit Awards program recognizes companies with the most comprehensive commitments to strengthening communities. Companies are evaluated by their corporate peers and local United Ways. Instron was also honored on a local level.
Read more

LABELS:
Community,
Did You Know?
Subscribe to:
Posts (Atom)