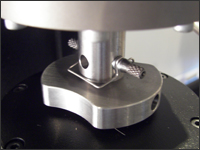
Grips Supplied with Locknuts
If the locknut is insufficiently tight, the forces experienced during a test, particularly a cyclic test, can cause backlash in the load string leading to errors in the test data. Before testing, make sure that you preload the load string, using a load greater than the expected maximum load, and tighten the grip locknuts while the load is applied. Read more
